Vertical machining center mold parts according to its role can be divided into forming parts and structural parts, forming parts refers to the direct participation in the formation of the cavity space of structural parts, such as concave mold (cavity), convex mold (core), inserts, line position, etc.; structural parts refers to the device, positioning, guidance, ejector and forming to complete a variety of action parts, such as positioning rings, keezers, screws, draw bar, ejector, seal, fixed distance pull plate The parts are used for positioning, guiding, ejecting and completing various actions during forming, such as positioning rings, grippers, screws, puller bars, ejector pins, sealing rings, spacer plates, puller hooks, etc. Commonly used structural parts see the next section. When planning the forming parts, the forming shortening rate of the rubber, the slope of the mold release, the craftiness of production and repair should be fully considered.
1. Forming shortening rate of rubber
The forming shortening of the rubber is influenced by many aspects, such as the variety of the rubber, the shape and size of the rubber part, the temperature of the mold, the injection pressure, the filling time and the holding time, etc. The most obvious influence is the variety of the rubber, the shape and the wall thickness of the rubber part. Different rubber materials have different shortening rate scale (see chapter 2, commonly used plastics), the detailed shortening rate according to the recommended value, if there are changes, need to be confirmed by the corresponding responsible person.
It is worth noting that the reference point chosen for 3D planning and 2D planning should be the same when increasing the shortening value for the same rubber part, otherwise it will make the 3D and 2D planning inconsistent.
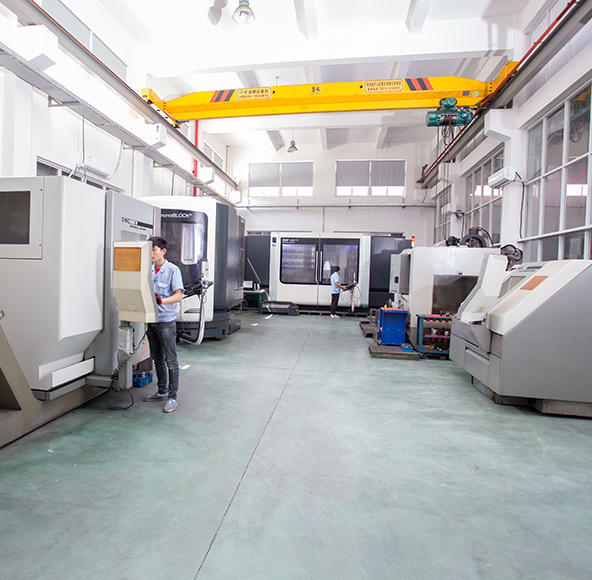
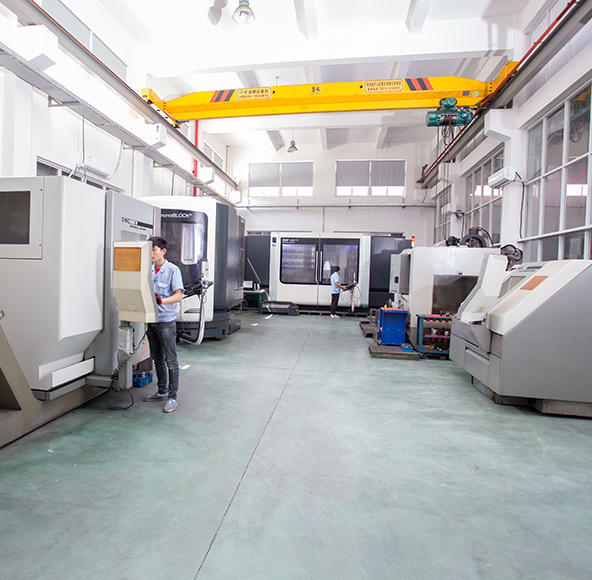
2. Release slope
Reasonable release slope is necessary for easy release and high quality appearance. In the planning of plastic parts, a more reasonable release slope is usually given. However, due to sometimes poor consideration, the plastic parts are chosen or formed with unreasonable release slope, which will definitely affect the appearance quality of the plastic parts, so the release slope of the plastic parts should be checked during the mold planning, and the unreasonable place should be discussed with the relevant person in charge. The following are the general requirements for the release slope.
(1) Commonly used rubber materials such as ABS, HIPS, PC, PVC, etc., the release slope of the outer surface of the rubber parts is chosen with reference to the following.
For small plastic parts with glossy exterior, the release slope is ≥ 1˚; for large plastic parts, the release slope is ≥ 3˚.
If Ra < 6.3 for etched surface, the release slope is ≥ 3˚; if Ra ≥ 6.3, the release slope is ≥ 4˚.
Ra < 3.2 on the outer surface of the flame-patterned surface, release slope ≥ 3˚; Ra ≥ 3.2, release slope ≥ 4˚
(2) Regardless of whether the bone position and column position of the inner appearance of the rubber part are planned to have the release slope, the release slope should be increased or modified according to the following requirements when the mold planning is carried out.
The thickness of the root of the bone position is less than 0.5t, ("t" is the wall thickness of the rubber part); the thickness of the top of the bone position should be greater than or equal to 0.8mm, and the detailed release slope is determined according to the confirmed thickness difference and the height of the bone position. If the release slope is required on both sides of the length of the bone position, a larger release slope should be selected without affecting the internal structure of the rubber part.
The requirement of column position is corrected according to the content of chapter 3 section 3.
(3) When increasing or correcting the release slope of rubbing or touching through position, choose the requirements of step type parting surface according to chapter 5 section 2, and if it affects the structure of plastic parts, negotiate with the person in charge.
3. Craftiness of forming parts
Mold planning, should strive to forming parts with good installation, processing and repair function. In order to improve the processability of the formed parts, the following points should be considered first.
(1) can not occur sharp steel, thin steel
(2) easy to process
Easy processing is the basic requirement of molding parts planning, mold planning, should fully consider the processing function of each part, through a reasonable combination of mounting to meet the processing process requirements.
(3) easy to fix the size and repair
For molded parts, the size of the parts may change should be considered combination structure, easy to wear the touch, rubbing position, in order to strength and repair convenience, should be selected to use the structure of the panel.
(4) to ensure the strength of the molded parts
(5) Easy to install
For the molded parts of insert structure, easy installation is the basic requirement of mold planning, and should prevent the installation of faults. For the shape of the regular insert or the mold has more than one shape and size of the same insert, the planning should consider to prevent the misalignment of the insert device and the same insert turning device. The often chosen method is asymmetric fastening or positioning of inserts.
With symmetrical fastening orientation, it is easy to have misalignment of insert 1 and insert 2, and easy to turn the same insert. The fastening orientation of each insert is not symmetrically placed, and the fastening arrangement of insert 1 and insert 2 is not the same, thus preventing the occurrence of misaligned devices and the same insert turning device. In addition, in order to prevent misalignment device, can also be used to locate the pin asymmetric arrangement of the method.
(6) Can not affect the appearance
In the planning of molded parts, it is necessary to consider not only the process requirements, but also to ensure the appearance of the plastic parts. Whether the plastic parts allow the existence of the pinch line is the premise of deciding whether the inserts can be made, if the pinch line is allowed to exist, the inset structure should be considered, otherwise, other structural forms can only be used. If the appearance of the plastic part allows the presence of the pinch line, the panel structure can be chosen to facilitate processing; the positive appearance of the plastic part does not allow the presence of the pinch line, and for processing or other purposes, the pinch line is shifted to the side wall, so that the panel structure is chosen. When the circular arc does not allow the pinch line, change the structure of the insert, the pinch line square displacement to the inner wall.
(7) Consider the cooling of the mold in general.
After the molded part is chosen to be inserted, if it is difficult to form local cooling, other cooling methods or the whole structure should be considered.